Advanced NDT Equipment
ADVANCED NDT SERVICES
Advanced NDT techniques are important . because they supply both increased productivity and the ability to reduce other ancillary costs. such as scaffolding, insulation removal, etc. Advanced NDT techniques help to solve industry problems cost effectively and efficiently. LSI ( large structure inspection ) survey used in lieu of scaffolding and Traditional NDT yielding equipment cost savings through less trade involvement and increased scan speeds.
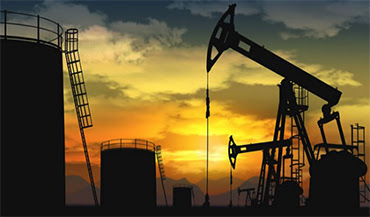
Oil & Gas industry
Advanced products, systems and services are used extensively in the Oil & Gas industry for a high degree of reliability, which supports improved safety, drives productivity, increases process availability and helps meet regulatory compliance standards. Our advanced technologies and techniques are utilized in Oil & Gas
operations on the following critical assets to identify potential damage mechanisms :
• Tanks
• Vessels
• Heat Exchangers and Condensers
• Piping
• Rotating Equipment
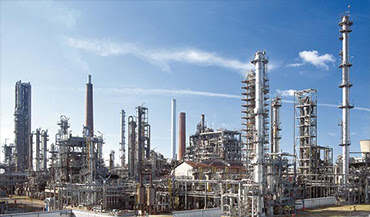
Petrochemical
Petrochemical and Power plants experience various flaws in their heat exchanges. As a result, Petrochemical and Power need to detect I.D and O.D. pitting, cracking and SCC, induced corrosion, erosion, support wear and cracking at or in the tube sheets, wear/wall loss.
Services
• Corrosion mapping
• Detection of HIC and SOHIC
• Weld Inspection of pressure vessels, piping and tubing
• Vessels and piping fabricated with composite materials
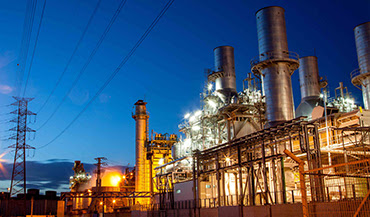
Power Generation
inspection of Assets such as Boilers, Piping, Tanks and Pressure Vessels. Problems identified from these inspections can help prevent unscheduled shutdowns and help trend problems so they can be safely monitored and tracked.
Services
• Pressure vessel and piping welds
• Turbine blades and Christmas tree designs
• Erosion/corrosion mapping
Phased Array Ultrasonic Technology
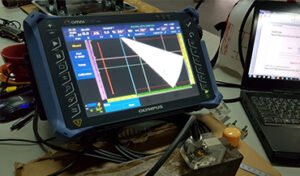
Phased Array Ultrasonic Testing
Phased Array is the latest advanced Ultrasonic technology that operates by a computer controlled excitation of individual elements in a multi-element transducer. In short, Phased Array generates multiple ultrasonic signals, in nanoseconds, that produce controllable angles, focus depths and/or wide coverage from one inspection point.
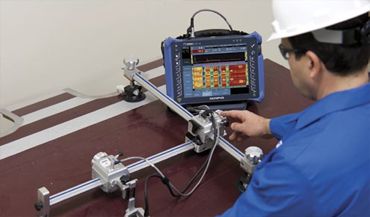
It has many advantages including
excellent repeatability, increased inspection speeds, more accurate results and the ability inspection speeds, more accurate results and the ability to inspect complex geometries.
interactive analysis of A-scans, B-scans,S-scans, and C-scans for multigroup and multiprobe inspections.
The technology also produces multiple measurements that are synchronized and cursor/ gate associated, making the detection, location and characterization of defects much more reliable and exact than the results obtained with conventional shear wave inspection.
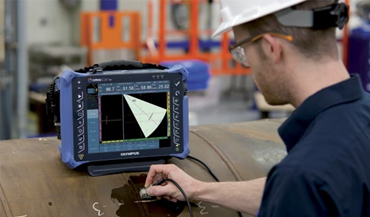
This technology has many applications
applications across a variety of industries including:
• Weld Inspection of pressure vessels, piping and tubing
• Vessels and piping fabricated with composite materials
• Pressure vessel and piping welds
• Erosion/corrosion mapping.
• Corrosion mapping
• Turbine blades and Christmas tree designs
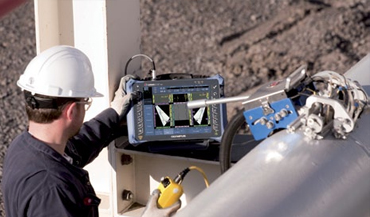
Phased arrays offer significant advantages over traditional radiography of welds as well:
• No safety hazards
• Inspection as soon as weld is cool
• Better defect detection and sizing
• Able to penetrate thick sections
• Compliant with all known codes
Time of Flight Diffraction (TOFD)
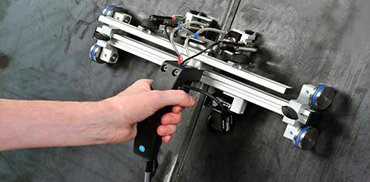
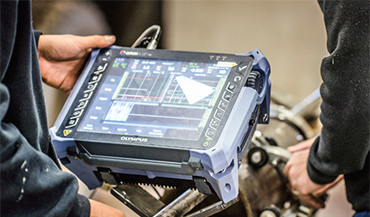
Phased Array engineers/technicians.
Our highly qualified automated ultrasonic engineers/technicians operate the system in both manual and automated scanning modes. automated pipe and vessel weld inspection or erosion corrosion surveys.
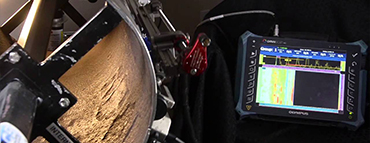
Phased Array generates an ultrasonic beam with the capability of setting beam parameters such as angle, focal distance, and focal point size through computer controlled excitation of the beam. it can be multiplexed covering large areas and the operator can vary the angle of the beam without moving the probe. Applications include weld inspection, complex geometries, defect detection and location, and sizing. the ability to record weld scans and to visualize the reflectors and their position within the weld makes it a qualified technology and an excellent choice for projects constructed to All ASME phased array code cases , ASTM E2700-09 ASTM E2491-06, AWS, API 1104 and API RP2X,CEN EN 583-6 , BSI BS7706 And more
Eddy Current Technology
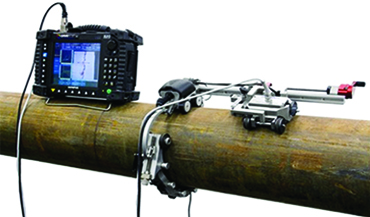
Eddy Current Technology
Eddy current inspection is leading the industry for in-service inspections on coated components. Eddy current has the ability to detect surface breaking defects such as in-service cracking under non metallic surface finishes.Services Division offers a complete range of inspection, training and QA/QC services. We integrate innovative technologies with conventional testing methods to ensure the integrity of industrial materials and components as cost effectively as possible. Eddy Current testing is based on measuring the impedance of a coil or inducing electrical currents (Eddy Currents) in a conductive material. Any changes in the coils impedance due to geometry, material changes, or discontinuities- such as pitting, erosion, corrosion, baffle fretting, cracking, and/or other anomalies will disrupt the flow of Eddy Current and produce a representative signal on the Eddy Current Testing instrument.
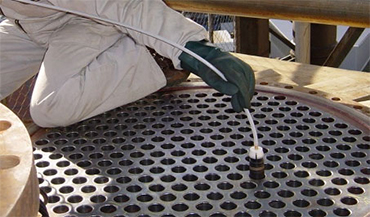
Eddy Current Applications:
Application Solutions provides highly qualified Eddy Current technicians . The equipment allows the technician to accurately and confidently inspect any tubing in Real-time, by allowing full length recording capabilities. This allows Data Analysis to be performed offline in order to assess damage with the customer.
Applications:
• Heat Exchangers • Condensers • Feedwater Heaters • AC Chillers (Air Conditioners)
Applications Advantages:
• Sensitivity to gradual wall loss, corrosion, pitting, erosion, baffle fretting, cracking and etc.
• Inspection of nonferromagnetic tubing.
• High rate of inspection (80 to 100 tubes per/hr).
• Can distinguish between I.D. and O.D. defect orientation.
Eddy Current has several basic advantages over PT including:
• More sensitive for detection of tight cracks
• Can inspect through paint coatings
• Much faster for small areas
• Detects SCC in stainless steel pipes
• Locates cracks in stainless steel vessels/tanks, turbine blades
Pulsed Eddy Current technology
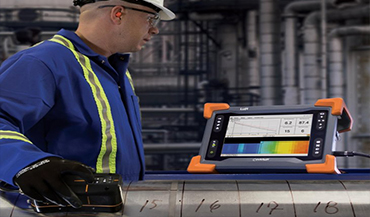
Pulsed Eddy Current
FAILURES DUE TO CORROSION
Failure of steel support structures, piping systems or vessels can be caused by corrosion of the steel under passive fire protection or insulation and visual signs of degradation may not be evident.
Pulsed Eddy Current technology can help detect such hidden corrosion before it becomes a potentially expensive and hazardous problem.
Pulsed Eddy Current inspection approach based on this technology checking for corrosion under passive fire protection or insulation. A detailed visual inspection is carried out to look for signs of degradation and Pulsed Eddy Current technology is used to measure the wall thickness of the metal behind the fire proofing or insulation.
ACCELERATED CORROSION
Degradation of steel can start when water penetrates the interface between the metal and the fireproofing because of faulty seals or inadequate construction. The corrosion products that are created may exert pressure on the passive fire protection and cause it to crack. This can allow more water to reach the steel, which accelerates corrosion.
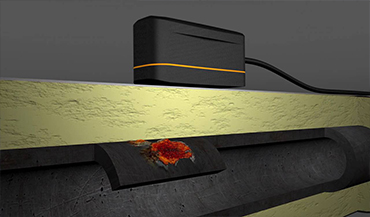
BENEFITS OF PEC TECHNOLOGY
• PEC technology can be applied in-service, so there is no need to empty the storage spheres.
• No need to remove the passive fire protection. PEC technology can measure through up to 250 mm of material including the reinforcement mesh.
• Performed in service during plant operation
• Monitor to assess CUI or FAC damage
• Accessibility issues minimized by using rope access Operators
PEC TECHNOLOGY APPLICATIONS
• For in-service wall thickness monitoring – monitor the corrosion rates of critical equipment to facilitate the safe extension of run times and the reduction of shutdown frequency and duration
• To annular rings: detect corrosion while atmospheric storage tanks are in service by measuring the wall loss of annular rings.
• In the splash zone: improve safety cost effectively when measuring caisson and riser wall thickness.
Readings can be made through marine growth and up to 20 mm of coatings and corrosion products.
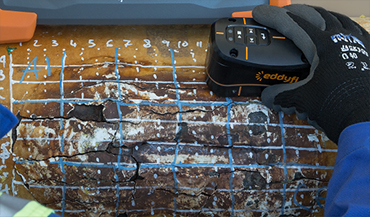
Corrosion Under Insulation (CUI)
Without an effective CUI protection program, the damage can be difficult to detect, harder to mitigate, and comes with even greater cost. As the industry’s truest one-source provider of asset protection solutions, We Have the resources, knowledge, and subject to implement and manage all phases of CUI program.
Visual & Qualitative Inspection
Our API-certified inspectors then conduct visual inspections to get a first look at the potential problem areas, after which they’ll determine and perform the appropriate qualitative inspection technique.
Inspection Preparation
Our expert mechanical service technicians prepare areas for quantitative inspection,through combinations of insulation removal, corrosion mitigation, and surface preparation.
Quantitative Inspection
We can deploy a variety of quantitative inspections to determine corrosion severity,including ultrasonic thickness, phased array, and radiography. Localized vs General corrosion, radiation concerns, and access to the asset guide the decision process.